JK APEX Front Axle ARMOR KIT

- PATENTED APEX truss: increased rigidity with peaked top design
- CNC precision laser-cut: lightweight, strong 1/8" mild steel construction
- CNC precision bent: ensures excellent fitment, easy welding
- 3D-modeled design: amazing fit, clearances with surrounding components
- 70% less welding: less warping, faster turnaround, lower costs
- Bent long seams: minimal time spent welding together
- APEX design: end-to-end axle reinforcement, industry first
- Dimpled holes: weight reduction, rigidity, and strength
- Weldable with MIG: requires moderate pre/post-heating
- Worry-free wheeling: up to 37" tires on stock JK axles**
- Strengthens weak axle sections: enhances durability
- Low profile design: compatible with slightly lifted vehicles***
- 1/4" steel LCA Skids, Inner C Gussets, HD Trackbar Brackets
- Reinforces or replaces weak axle components
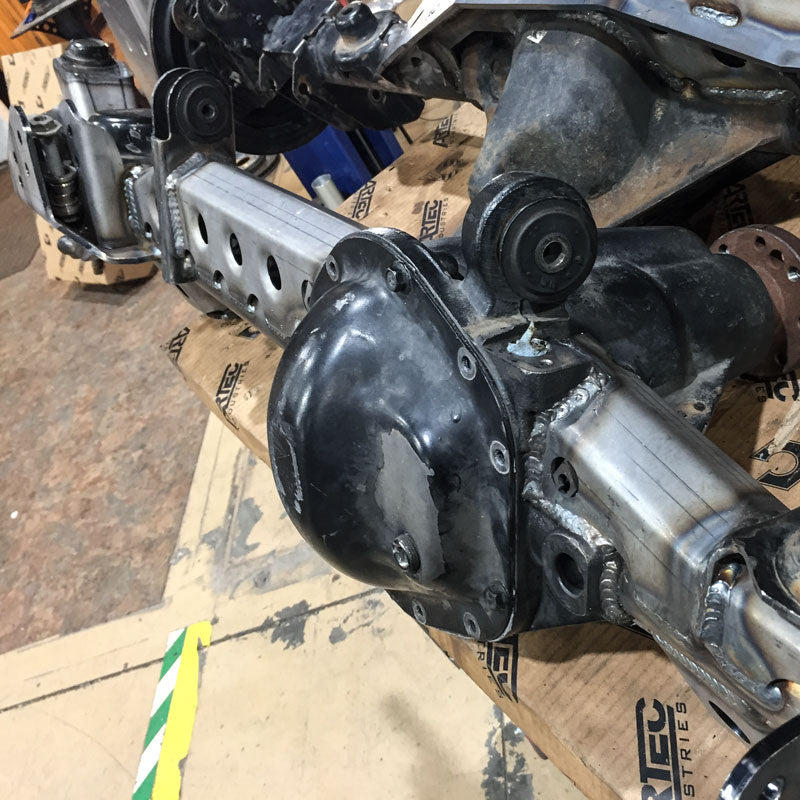
Upgrade your factory JK front axle with Artec Industries' comprehensive armor kit, designed to reinforce the weakest parts and ensure maximum durability. The kit includes the APEX Front Axle Truss, Front LCA Skids, Inner C Gussets, and APEX Heavy Duty Trackbar Bracket. The JK APEX Front Axle Truss features a unique, peaked shape top for extra rigidity, weight savings, and simplified installation. This design extends underneath the coil perches, forming a complete end-to-end truss—an industry first in OEM axle applications. JK Front LCA Skids provide serious abuse protection for your JL front axle lower control arm brackets. These 1/4" thick, precision-cut components ensure easy installation and enhanced durability. JK Inner C Gussets reinforce your front Dana 30 or 44 JK Inner C's, adding rigidity with 1/4" thick, precision-cut components. JK APEX Trackbar Brackets address the weak factory axle side tracbar bracket, a common cause of "death wobble." Designed for compatibility with the APEX Truss, these heavy-duty brackets eliminate issues and raise your steering stabilizer for greater clearance. Choose between STOCK HEIGHT for smaller lifts with adjustable tracbars or RAISED HEIGHT for taller lifts requiring a DRAG LINK FLIP. The Artec Industries armor kit offers the ultimate protection and easy insurance for your factory Jeep axle.
- JK3055 -Use on JK Sport/Sahara (Dana 30 front axle) with over 3 inch lift using DRAG LINK FLIP KIT
- JK3056 - Use on JK Sport/Sahara (Dana 30 front axle)with under 3 inch lift using factory trackbar mounting location
- JK4455 - Use on JK Rubicon (Dana 44 front axle)with over 3 inch lift using DRAG LINK FLIP KIT
- JK4456 - Use on JK Rubicon (Dana 44 front axle)with under 3 inch lift using factory trackbar mounting location
Notes : If your lift replaces your trackbar and mounts to the factory axle bracket (typical with a lift that includes an adjustable trackbar), choose FACTORY HEIGHT BRACKET. If you are doing a

Reviews

Install Instructions
While we're working on the detailed instructions, here's some tips on installing your APEX truss. Refer to online pictures for orientation of the truss.
STEP 1. Unpack contents of shipment. Remove axle from vehicle for best results and easiest installation. Prior to mockup make sure axle is clean and uninstall any oem and aftermarket bolt-on accessories that may conflict with truss installation. Remove axle breather hose and uninstall any electric locker wires from casting. This area will be welded so care should be taken to prevent these components for melting.
STEP 2. Place parts 1 and 3 on the axle around the pumpkin. These parts should drop right on and self-center. Part 2 requires a little more work. If you are keeping your factory trackbar bracket, you will need to remove some material from part 2. Using a cutoff wheel, cut along the laser etched lines which make a trapezoid shape. If you are using a replacement Artec trackbar bracket, no cutting of the truss is needed. Place the tip of the truss that contacts the coil bucket on the coil bucket and rotate the truss down sliding past the UCA bushing. It may require a little force to pop past the bushing. Part 4 goes under the passenger side coil bucket. If you are keeping the factory trackbar bracket, you'll need to trim this bracket on the etch lines as well. Once trimmed, the truss piece will slide in from the backside over the shock brackets...it may take some work to shimmy it in there. If removing the factory trackbar bracket and using an Artec trackbar bracket, this piece can easy slide in from the front. Part 5 slides in from the front under the driver side coil bucket.
STEP 3. Using a marker or paint pen, indicate the areas on the axle where the truss touches the axle to prepare for welding. Remove truss pieces from axle. Using an angle grinder with either a flapper disc or wire wheel brush, clean the surface of the axle tube, casting, upper control arm mount, and coil perch until bare steel is exposed. Clean surfaces on drivers side casting, tube, and coil perch in a similar fashion. Repeat step 2 and place all truss pieces back on axle.
STEP 4. Prior to welding, ensure that the bottoms of all the truss pieces are in a straight line all together. The long truss can sag a little near the UCA mount so push down on the part over the casting and it'll straighten out. Place tack weld on truss pieces to hold all in place. Double check all truss pieces are straight.
STEP 5. Begin welding small strips of truss that touch the axle tube. You want to move around to different parts of the axle as you weld so you don't heat up areas too much. Place a welding blanket over welds so they do not cool too quickly.
STEP 6. To weld truss to cast section with best results, preheat casting evenly around where truss contacts to approximately 400 degrees. DO NOT HEAT UNTIL GLOWING RED AS THIS MAY DAMAGE THE CASTING. Once preheated, weld truss to casting before it cools. For best results, use a needle scaler or peening hammer to relieve the weld directly after welding. Post heat the area to approximately the same temp you used to preheat. Wrap axle in a welding blanket to slow the cooling process, the cooling should be slow (18-24hrs.) and uniform. (The idea behind this method is to relieve the stresses in the materials prior to welding, and ensure that the plate steel does not cool quicker than the cast resulting in stress cracks.)
STEP 7. When completely cooled, check for any cracks in weld especially around the casting. If cracks are discovered repeat the necessary steps above, grinding out any cracked welds and prepping the area.
STEP 8. Once axle is ready, paint truss and axle where bare steel is exposed to prevent rusting. After paint is dry, reinstall axle breather hose, electric locker wire, and any other components. Install axle according to manufacturers specs.
Full Instructions Coming Soon
Click image above to view Installation Instructions


Community Discussion