Low Profile Ford Kingpin-Balljoint Front Truss (1985 - 1997)

- Fits Ford Kingpin axles 1985-1991.5 and Balljoint axles 1992-1997
- 3/8" thick mild steel truss top and 1/4" mild steel gussets. CNC cut for great fitment
- Low profile design for more uptravel and better clearance for oil pans
- Spans entire length of axle for complete reinforcement - not just for links
- Reinforced using interlocked 1/4 thick gussets for maximum strength and easy assembly
- Internal gussets for additional strength and rigidity
- Main interlocking gussets wider than Gen1 trusses, adding overall strength
- Truss clearanced for differential breather tube (adapters needed)
- Sleek design means easier fitment and less interference with vehicle components
- Made in the USA
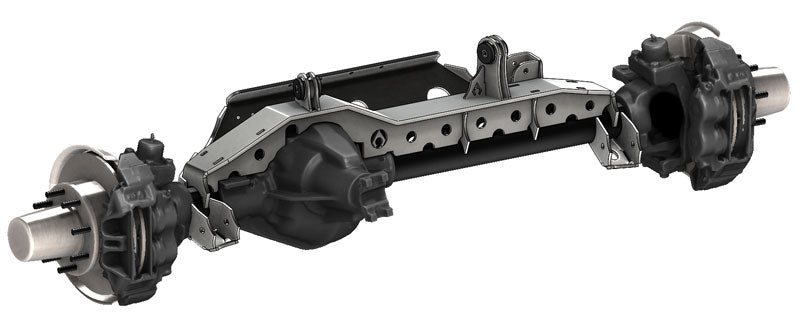
Artec Industries announces the next generation of trusses with additional strength and functionality. The new design has a super low profile truss top that bends around the differential, allowing for more uptravel, better clearance, and increased strength. Ideal for vehicles needing more clearance or building low center of gravity vehicles.

Reviews

Install Instructions
THIS KIT INVOLVES EXTENSIVE WELDING AND
GENERAL FABRICATION SKILLS. ONLY COMPETENT WELDERS SHOULD ATTEMPT TO INSTALL
THIS KIT.
Tools Required :
Safety Glasses, Gloves, Tape Measure, Socket Set, Wrenches,
Wheel chocks, Jack, Jack stand. Cutting
Tool of your choice (Sawzall, Grinder, plasma, cutting torch) Welder.
Step 1:
Inventory that you have all of the parts for your order If you are missing parts
or have incorrect parts contact Artec Industries Immediately @
(855)-278-3299 M-F from 8am-5pm MST If it is after those hours please Email
Sales@Artecindustries.com
Step 2:
Place wheel chocks at the rear wheels of the vehicle. Break free lug nuts on rear wheels (Do not
fully loosen or remove lug nuts yet.)
Step 3:
With the vehicle sitting on the ground, Measure your ride
height at the frame and height of the centerline of the axle, Also take measurement
of your wheel base.
(Make a note of this for later.)
Step 4:
Jack up the front of the vehicle and set the axle on Jack
stands, Remove the rear wheels from the vehicle, With the wheels removed Jack the vehicle up
again. Securely place tall jack stands
under the frame behind the LCA or Leaf
spring mounts at the previously measurement of ride height. Place a 2nd sent of
jack stands under the front axle.
Step 5:
Remove the existing front axle from the vehicle
Step 6:
Prep axle the truss will be welded onto by removing all
mounts and paint/ rust. Once the axle is
prepped. Slide new axle under the vehicle and place on jack stands at the
measurement of what the centerline height was at ride height also make sure it
is set to the wheelbase you will be using.
Step 7:
Using another jack stand or block of wood set under the Pinion
of the axle, Set the Caster angle and pinion to desired angle of your build to ensure it
does not get changed . Now place the truss on top of the axle so it is level
with the ground and not tilted forward or backward (If
your truss is angled it can cause upper arm mounts or the truss to twist off
under load) You may need to trim
some gussets on the truss to allow it to sit level depending on your wheelbase
and pinion angle. (Ford 9” trusses will need to be trimmed to fit your axle)
Step 8:
With the truss set level on top of the axle tack weld The
truss ends to the axle tubes.
Step 9:
With the truss tacked into place Pull the axle from under
the vehicle to allow more space for welding.
Once the axle is pulled from under the vehicle. Heat the axle to about 400 degrees Start
to weld the gussets to the axle and
truss .When welding, Start on one side of the axle, Weld a small amount, Then
move on to the opposite side of the axle to allow each side to cool. This will
help prevent warping .Stitch welding is preferred and welding every inch of every seam is not
necessary. Grind and clean the rosette welds on the axle. If your truss has a
bridge you may need to Trim the bridge depending on your pinion angle and weld
it to the truss. (Optional) Stitch weld the axle tubes to the ends of the casting for added
axle strength and to prevent the axle tubes from twisting. If you have
any Control arm mounts, Shock mounts, Coil over tabs, Track bar mounts that
need to be welded on to the axle you
will need to place the axle under the vehicle on jack stands at ride height and
desired wheelbase an weld them on at this time in their proper location for
your specific build. Once all of the
welding is complete you will wrap the
axle in a welding blanket to slowly cool overnight.
Step 10:
Clean the Truss and axle of any machining oils and Prep for
paint or powder coat.
Step 11:
Install the axle back under the vehicle and place on jack
stands. Install the wheels on the vehicle and tighten the lug nuts (Do not
torque them down yet.) Lift the vehicle
and remove all of the jack stands and set the vehicle on the ground. with the vehicle on the ground check all of
the bolts and lug nuts are torqued to proper specs. we recommend drawing a line
on the nut and bolt heads and where they are mounted for quick reference when
checking for tightness after 50 miles .


Community Discussion